High-Speed Bulk Bag Filler
Model 5200
Model 5200 is highly automated and our fastest bulk bag filler. It feeds powders and granules into bags weighing as much as 3,300 pounds at up 25 per hour. The use of slide gates, augers, or rotary air locks for feeding greatly increases its material range. Pallets are automatically destacked, squared, and indexed on the weighing scale. Empty bags must be hung manually but all other functions are automatic. An inflatable seal cuff securely holds the bag for dust-free filling. The digital scale keeps weights accurate and within tolerances. After filling, bag strap holders release the bag, index it, and place it on an accumulation conveyor while the next pallet is loaded.
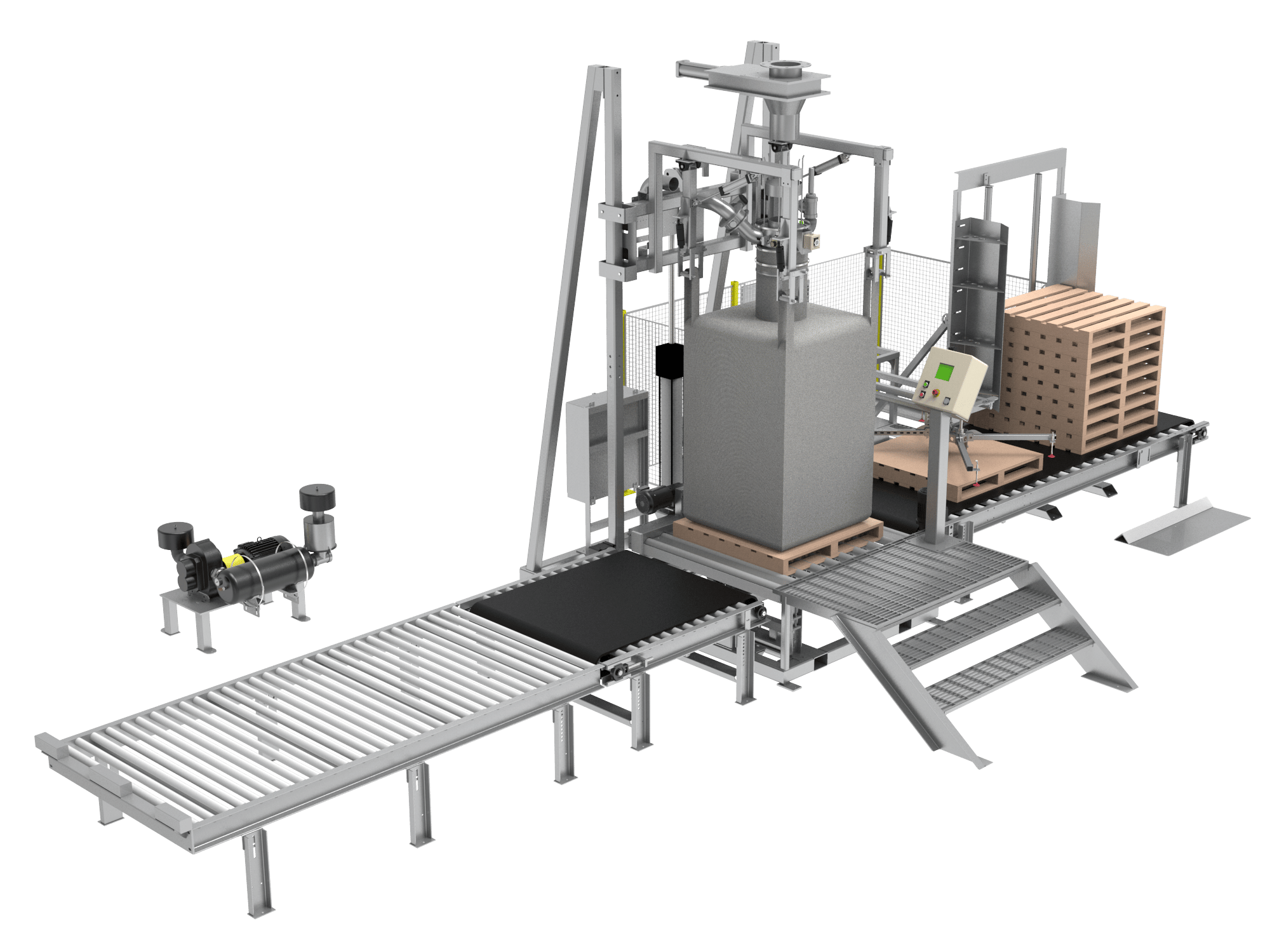
Examples of Materials Bagged with this Machine
Mortars, hydrated lime, gypsum, bentonite, barite, pigments, fertilizer, plastic pellets, plastic resins, calcium carbonate, starch, corn flour, oat flour, powdered sugar, hard grains
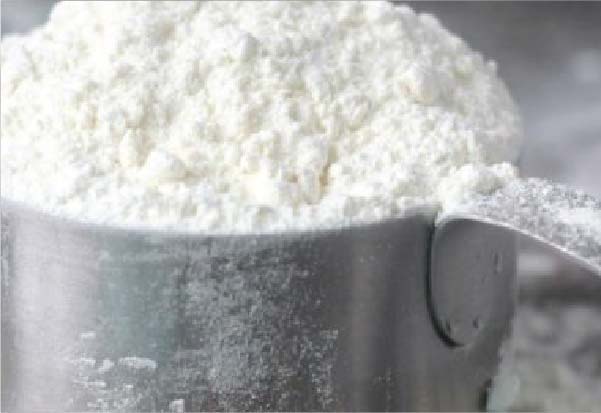
Powders
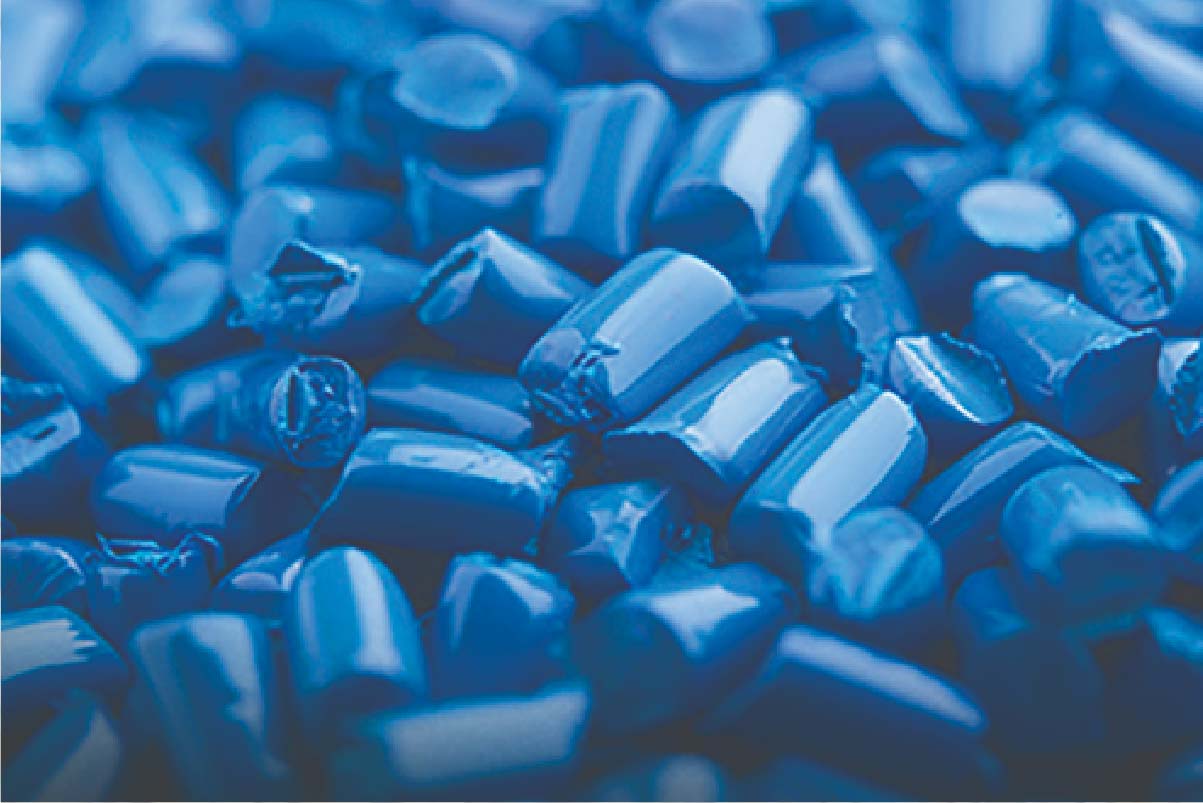
Granules
Specifications:

Bag filling weight range: 1,100-3,300 lbs. (500-1,500 kg)

Production rate: 1-25 bags per hour (material and bag size dependent)

Material density range: 35-150 lbs. (15.9-68 kg) per cubic foot

Operating modes: Manual and semi-automatic (operator assisted)

Bag types: Spout type poly woven bags, super sacks, and corrugated boxes (Gaylord, Octiboxes)
CHOICE BAGGING EQUIPMENT
4804 N Main St,
Taylor, TX 76574
Hours
Monday-Friday 8am-5pm
Saturday & Sunday: Closed