We recently supplied one of our auger fillers to a producer of specialty sugar in central New Jersey. Shortly after startup, the customer began calling our bagging equipment service department complaining of poor bag weight accuracy that was way out of range of tolerance.
The initial assumption was that there must be a problem with the weight indicator or load cell, so replacements were sent to the plant to change out. Neither of these solved the problem and the weight problems continued. After a few more attempts to solve the problem over the phone, we decided that a technician be sent to the plant to diagnose the problem. The immediate presumption is that since the weight accuracy was poor then there must be some problem with the machine.
Upon arriving at the plant, our technician first calibrated the machine and then checked it for repeatability. Repeatability means starting with the scale at 0.00 then adding a known weight (50.0 pounds as an example) and making sure that the scale climbs to that weight and returns to zero several times in immediate succession. The scale passed this test.
Next, our technician had the customer load product into the machine. The first two bags came off the machine within the specified weight tolerance and then soon after the weights began to become erratic and get progressively worse. Our technician again used the known test weight to check the calibration of the machine. This time, the scale would not repeat. The only difference between the first calibration and scale check was that product had been loaded into the machine.
The Case of the Melted Sugar
At this point, our technician made the assumption that somehow, the product itself must be influencing the scale. Knowing that one of the characteristics of sugar is its tendency to melt when heated or pick up moisture from the air and get hard, our technician wondered if this could be the problem.
So he removed the filling spout of the machine and noticed that it had hardened material caked upon its interior walls. This is a problem for an auger valve bag filler as the auger within the filling spout is rigidly mounted to the framework of the machine and is not part of the weighing scale. Yet the filling spout that surrounds it is what the bag hangs from to be weighed and is part of the scale. Any solid contact between auger and spout which was the core problem in this case would make results suffer greatly. Because once the material hardened inside the spout, every time the auger would rotate it would push against that hardened material, and thus the spout and wreak havoc on bag weight accuracy. We alerted the customer so that he could adjust his cleanout procedures to make sure that the product would not build up on the inside of the spout.
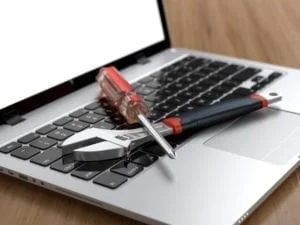
Next, our technician looked to the controls of our machine to see what could be adjusted to prevent the sugar from heating up inside the machine. First, he looked at the variable speed auger drive and slowed its speed down so that the auger would not generate as much heat and friction as it rotated. Then, he turned the auger reverse time in our motor control panel to zero. The auger reverse function is designed to provide a sharp stop to material product flow by reversing at the end of the bag fill and pulling the material back away from the end of the filling spout. Based on his considerable experience, our technician made the assumption that the auger reversing function could be contributing to the compacting of the material inside the machine because as it reverses, it reverses the product in the spout into the product in the housing. The thought was that if the material was hot or sticky, that reversing the auger might exacerbate the problem. So he turned the reverse function off.
With the spout cleaned of buildup and these two changes in place, our technician asked for the customer to try filling some more bags. The results were markedly improved. Bag weights averaged within 0.3 pounds of the target weight. Fill times were still within expectation. However, our technician knew that the machine was capable of better.
Next, our technician began looking at the feed system of the machine. It was being poorly fed. First, it only had the capacity to hold a couple of bags worth of material. Second, it had no level controls to indicate when there was sufficient material above the machine to fill a bag. Third, the bin was built such that the material bridged within it, so that only a small portion of the material within it would empty down into the filler and the rest would stay stuck inside the bin. And finally, the bin was being fed by a screener that could not screen the material as fast as our auger filler could bag it.
The small bin coupled with the lack of level sensors and the fact that the bagger was faster at emptying the bin than the screener was at filling it meant that our filler was at times being starved for material. Our technician pointed this out to our customer and helped them to install a vibrator on the side of their hopper to knock the material loose from the walls of the hopper and improve its feed to the machine. Our technician also trained the operators to make sure that the hopper was full before beginning a bag fill on the machine.
With this simple adjustment and no further adjustments having been made to the bagger itself, weight accuracy further improved to within 0.1-0.2 of the target weight. The presumed problems (the machine) turned out to be a combination of educating the customer on the importance of cleanout and product flow and assisting them with finding the ideal set of operating parameters to make the machine run at its peak capability.
A good technician can considerably shortcut learning curves with his vast knowledge of machines and applications. Sometimes subtle clues that may seem unimportant turn out to be the things that help identify the solution to the problem. Sometimes these things can be divined over the phone. But sometimes, these clues do not come through the phone either because the customer disregards what he is seeing as unimportant or doesn’t understand what they are seeing. Sometimes, there is no substitution for experience, a trained eye, and a skilled hand.
Recent Comments