Regardless of which type of bag an operation uses – valve, open mouth, or bulk bag – the ultimate goal of virtually every industrial bagging operation is to fill and seal as many bags as possible cleanly and accurately within a specified time period. Yet while the goal is simple, bagging dry bulk solids can often be tricky in implementation.
There are interrelated factors that must be balanced in order to ensure a successful operation. Three of these factors work together like the legs of a three-legged stool. If one is missing or not in balance with the others, the stool will not set right or possibly topple over. These three factors are:
- Product
- Bag
- Machine
A Corollary Relationship
There is a direct and corollary relationship between these three aspects in every bagging application and the right combination can mean the difference between success or failure. The concept is simple; if one pillar is out of balance with the other two, the results of the entire installation will suffer. Furthermore, a small change to any one of them – the product, bag or machine – necessitates a change in one or sometimes both of the others.
The Cause of Many Problems
It’s very common to blame poor results on bagging machinery, but oftentimes bagging equipment is not the largest problem. It’s just as likely that product characteristics have changed (or in some cases continuously change). Working in partnership with a competent bag supplier and machine manufacturer can help to steer clear of common pitfalls and avoid hazards that might otherwise produce poor results.
An Example of a Powder Bagging Problem
As an example, consider a producer of a powdered material that decides to upgrade its packaging machines. The producer’s representatives search for and find a machine that has the combination of features they are looking for at a price they can afford. They conduct testing on the machine prior to purchase and all projections look excellent.
The new machine is installed and put into operation. At first glance, all appears well. But soon operators complain that the machine is spilling a large amount of product during the filling process or dusting excessively. Or perhaps the bag weights are out of specifications for weight tolerance. Any of these problems could be caused by the bagging machine itself. But they could just as easily be caused by a bag that is too small (one that fills to the volume before it fills to weight) or the bag could be sized right and the bagging machine could be performing properly and the product is being over-aerated by upstream process equipment or somehow the product is being inconsistently fed to the filling machine. The point is that many times the cause and effect of problems within a bagging application might or might not be what they appear to be. There is a balance that must be achieved between bag, machine and product to make good results possible.
Pillar #1, The Product
The installation of any new industrial bagging equipment should begin with a thorough analysis of the product and its properties as well as a careful review of the environment that the machinery will be installed in. Crucial traits such as flow property, bulk density, moisture content, de-aeration characteristics, compaction properties are all important factors in choosing the correct machine for the application.
Additionally, the design and construction of the silo/supply bin and the product feed system should also be reviewed to ensure that the bagging machine is being supplied with material that is consistent and is not being subjected to influences of upstream equipment that will change the products density, flow characteristics, and consistency.
Finally, sometimes product manufacturers will change the formulation of their products after their equipment has been operating for a period of time. When this happens, it’s important to test and analyze the new material mix to determine what the ideal bagging machine settings and bag characteristics should be to use with the new product formulation.
Pillar #2, The Bag
Although it does not seem difficult, choosing a bag that is engineered correctly for a given application is not as straightforward as it may appear. Frequently when a producer experiences poor results, the root cause of the problem is a bag that is not appropriately designed for that specific application.
This is not to say that the problem is the quality of the bag or the producer of the bag for that matter. For instance, a common problem we see on a regular basis is that bags are sized to fit the packed (non-aerated) bulk density of a given material while most times those same materials are fed into the bag at their loose (aerated) bulk density. In practical terms what this means is that when the product is moved mechanically or pneumatically, it is entrained with air and when that air is mixed with the material the bulk density is temporarily lowered.
The problem is that most people sell their products by weight, not volume. The dilemma they face is that if they sized their bags to fit the loose (aerated) bulk density of their material, the bag would look like a raisin when the product settled and returned to its non-aerated state. But to make matters worse, frequently they will use the bag and the bagging machine as a mechanism for compacting the material into as small a space as possible.
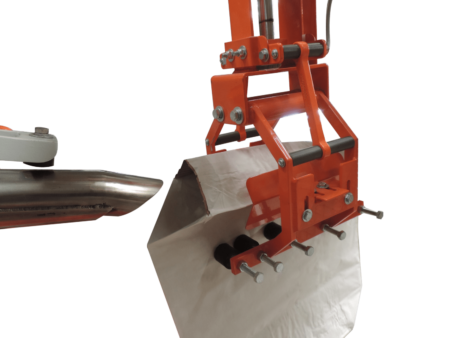
On the surface, it makes sense. A dense package looks better. It travels well and is less susceptible to load shifting during transit. And the more material that can be fit into a smaller space, the less it will cost to ship. Yet, the simple fact is that a bag that fills to the volume before it reaches the target weight will produce a list of negative and unwanted side effects. The bag will be full but the bagging machine that is designed to fill by weight will continue to attempt to deliver material into a bag that has no more room to fit it. The result is product spillage and dusting and bag weights that are out of tolerance.
Perhaps the more critical of the two is the bag’s ability to release air pressure, and that depends largely on the materials used to fabricate the bag. Many factors must be considered here, including whether the bag is made with traditional paper, high-performance paper, plastics, or a combination. The weight of the material and the number of layers also need to be considered. The ability of a bag to release internal air pressure is greatly impacted by the inside mechanics of the bag, like whether there is a layer of polyethylene (PE), to what extent the PE is perforated or sliced, and wherein the layer sequence the PE is inserted. The ability of the bag to release air pressure subsequently impacts filling speed and overall machine performance. For instance, in the case of air packers which work by creating an imbalance of air pressure between high pressure (the pressurizing chamber) and low pressure (the bag), if the air pressure inside the bag equalizes with the pressure in the pressurizing chamber of the machine, the product will stop flowing or flow slowly.
The second factor, consistency in the quality of the bag’s construction, can impact the filling process in three ways. First, in automated applications, if bag tolerances vary from bag to bag due to loose manufacturing tolerances of the bag manufacturer, the machine might have issues consistently placing the bag on the spout for filling. This could also affect the way they stack in the magazine, which can lead to misfeeding in the system. Finally, if there are issues with the quality of the bag or inconsistency in characteristics like perforation, efficiency can be compromised due to poor de-aeration.
Sometimes a bag change may have nothing to do with a supplier but is instead the result of a well-intentioned machine operator who sees an opportunity to save a penny or two per bag by making a change. Or perhaps the company’s purchasing department decides to switch to a bag with fewer layers.
Regardless of the reason, the company needs to step back and consider how the change will impact efficiency and make adjustments to the other two points of The Bagging Triangle to compensate.
Pillar #3, The Machine
The key to machine selection is to work with a manufacturer who understands the three pillars of bagging. A tell-tale sign of manufacture that understands the relationship of these three elements within a packaging process is one that offers to test product bag and machine together in order to make competent equipment recommendations.
Test Samples of the Product on the Machine
Although there are some straightforward applications that do not require upfront testing (like bagging corn or rice), the process typically starts with the machine manufacturer requesting a small product sample from the customer to analyze.
If the manufacturer’s initial analysis of the product matches with his understanding of the application, customer requirements, and the customer’s available budget, it is then a best practice to have a larger sample of the material sent to the manufacturer so he can set up a simulated product run of the material under a load of the customer’s actual product tested on the customer’s actual bag.
Testing the product is a critical step that helps define the product characteristics, the bag’s filling behaviors, and additionally to identify any previously unforeseen issues that were not considered in the original analysis of the application. From there the machine manufacturer can identify and define the proper filling technology to achieve the ideal productivity level. In addition, this testing helps determine optimal filling rates, how many spouts are needed to hit those rates, and what settings will need to be maintained on the machine to achieve them.
The initial setup is only the beginning. As a machine operator or company makes changes to the bag or the product, it is imperative that they evaluate the effect of those changes and adjust parameters on the machine to maintain balance. Before making the machine adjustments, it’s always wise to consult the manufacturer. Even well intentions changes can produce negative results if consideration is not given to how product and bag must also be altered to balance those changes.
In conclusion, it is the sum of product, bag, and machine that creates the conditions for optimal efficiency, productivity, and profitability. Working in partnership with competent bag and equipment manufacturers to find the right combination of product, bag and machine is imperative to the success of the application and ensure that high-quality results are achieved.
Recent Comments